The large panel and sky deck system is revolutionizing housing construction by providing faster, more efficient, and cost-effective methods for concrete pouring and forming. These systems are widely used because of their simplicity, speed, and the enhanced quality of the concrete they produce. By leveraging the capabilities of the large panel and sky deck system, construction teams can streamline operations and significantly cut down on labor costs. As a result, these systems help reduce both time and expenses in housing projects.
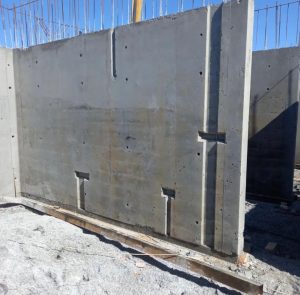
Introduction to the Large Panel System
The large panel formwork system offers a revolutionary alternative to traditional modular steel formwork. Unlike smaller panels, these larger formwork panels reduce the need for numerous connecting components such as pins, wedges, and scaffolding. This change simplifies construction and accelerates the installation process, ultimately leading to substantial cost savings.
Furthermore, transporting these large panels is more efficient, further lowering logistics costs. The construction industry has widely adopted this formwork system because it speeds up the installation process and significantly improves concrete quality. By implementing advanced formwork technology, buildings with a base of 60 to 80 meters can be prepared for concrete pouring within just four working days.
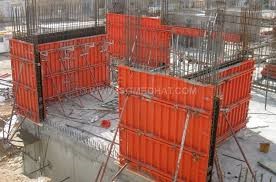
Benefits of Large Panels
The large panel system offers several advantages over traditional modular systems. These molds feature a robust, one-piece design, eliminating the need for clamps, scaffolding tubes, and pins. This design not only accelerates the construction process but also ensures that both internal and external walls are molded and concreted simultaneously in one integrated operation, avoiding seams and cracks.
The high load-bearing capacity, ease of implementation, and reduced setup time make the large panel system a preferred choice for construction.
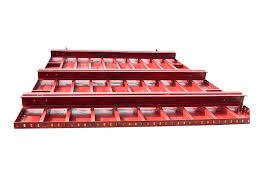
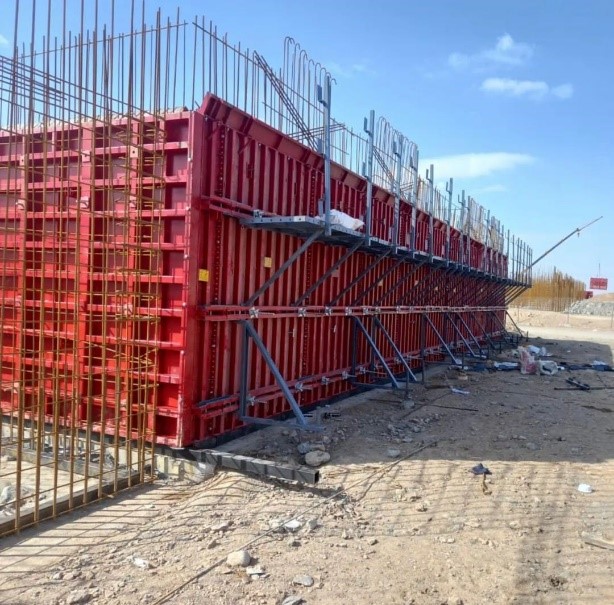
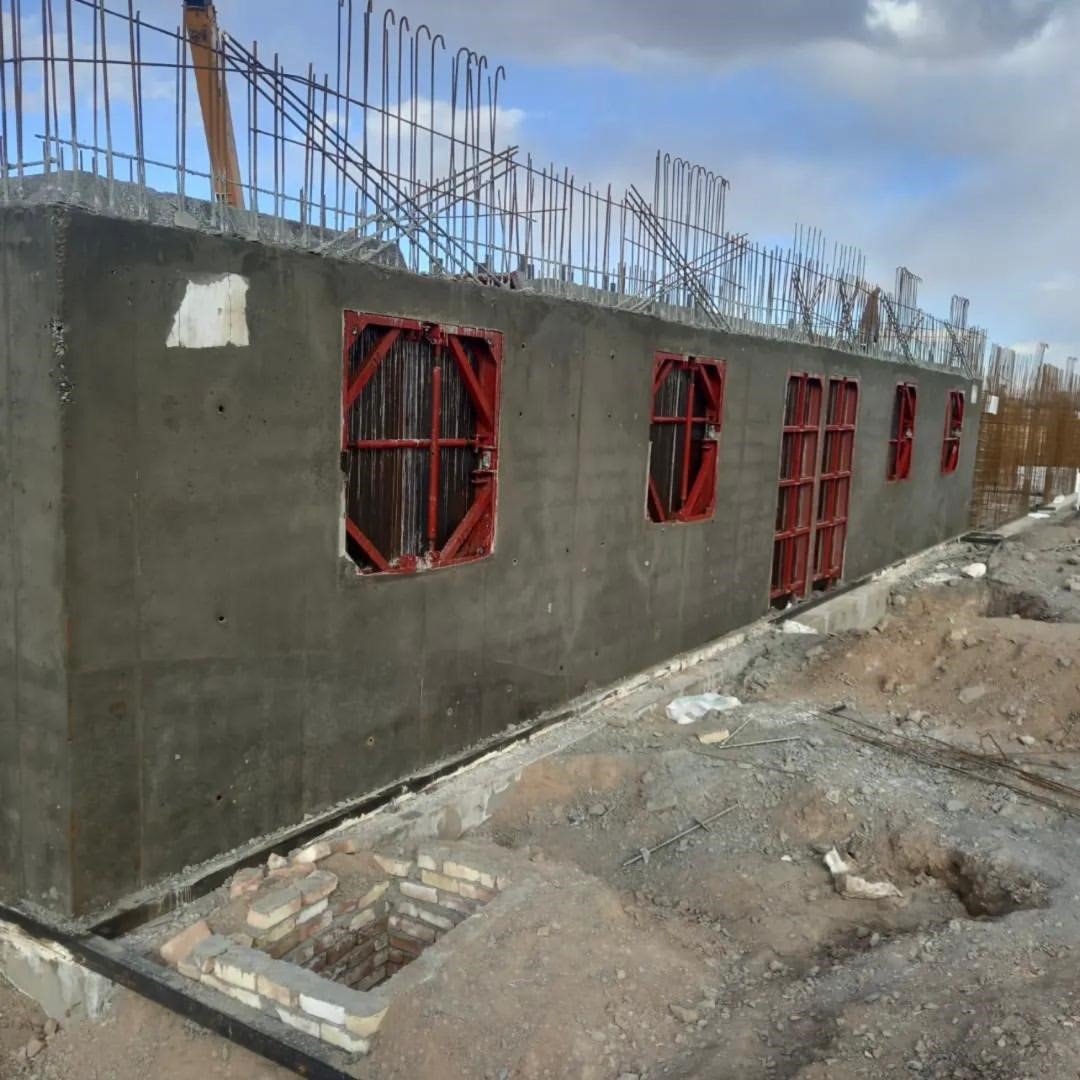
Step-by-Step Process of Using the Large Panel System
Step 1: Panel Pre-assembly
After reinforcing the walls according to the layout plan, the panels, each measuring 4 or 5 meters, are pre-assembled with all necessary accessories such as the concreting platform, vertical adjustment brackets, and shotcrete. Once these panels are ready, workers transport them to the construction site. Within just two days of assembly, the walls of a 120-square-meter building are prepared for concrete pouring.
Step 2: Concreting
Once the panels are in place, workers begin the concreting process. During this stage, it is essential to ensure that the panels are securely fixed and that all braces or back brackets are tightened properly. Proper control and adjustment during this phase guarantee that the concrete attains the desired strength.
Step 3: Panel Removal and Reuse
After the concrete sets, workers release the panels from the molds. The 4- and 5-meter panels can be easily transported to the next floor or block using a crane, without requiring major changes in the disassembly process. Workers connect the panels with simple frog pins or wedge joints, allowing for quick and efficient reuse.
Although the initial cost of these large panels is higher than that of modular molds, their ease of use, safety benefits, and reduction in labor and material costs make them a highly cost-effective option.

Sky Deck System: Efficient Roof Formwork
The Sky Deck system is designed specifically for molding roof slabs and flat ceilings. This system uses lightweight panels (typically 100 x 150 cm) along with unique header components, ceiling support jacks, and shoulder elements (also known as racks). Two people can install up to 100 square meters of these panels in one day, significantly cutting down labor costs.
Features of the Sky Deck System
- Fast and Easy Installation
- Lightweight Components
- High Safety Standards
- Easy Separation of Ceiling Panels
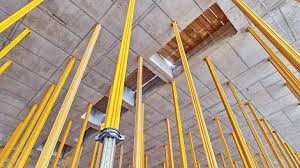
Step-by-Step Process for Installing the Sky Deck System
Step 1: Preparing the Roof
The process begins by preparing the roof with special jacks, which are anchored vertically to the concrete wall. One worker connects the main beams to the jacks, securing them to the ground jacks. This process is repeated for each beam to ensure stability for the upcoming panels.
Step 2: Installing Ceiling Panels
The second worker places the ceiling panels on the beams while the first worker continues to install the beams. This process is repeated across the roof slab. The Sky Deck system allows workers to quickly and securely install the panels, followed by concreting.
Step 3: Concrete Pouring and Separation
After the concrete sets, the unique head jacks (called drop heads) of the Sky Deck system allow the panels to separate from the ceiling. A simple blow of a hammer releases the panels by 6 cm, enabling workers to reuse them quickly in the next phase of construction.
This system can mold slabs up to 35 cm thick, ensuring high-quality and durable concrete roofs.
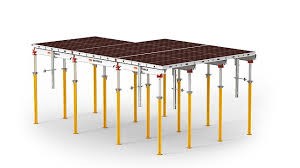
Also, you can visit our products section to explore our full range of high-quality solutions for housing and construction projects.
Conclusion
Both the large panel and sky deck system provide significant advancements in construction, especially for housing projects. These systems save time and reduce costs while improving the structural integrity of concrete components. By utilizing the large panel and sky deck system, builders can ensure a smoother, faster construction process with high-quality results. Their ease of use and rapid implementation make them indispensable tools in modern construction.
For more information on how to implement these systems in your next project, contact our team.